
PipePillo has undergone extensive testing The ideal pipeline support is something that is easy to use, requires little oversight during placement, and mitigates the risks described above (ovality, hard spots, denting, uneven settlement, soil migration).įigure 4. In the areas where the bedding has entirely migrated away, the pipeline rests unsupported on rocky trench bottom – the very thing the bedding was designed to avoid. Soil migration may occur at different rates along the length of the pipeline which results in an uneven trench bottom and contributes to excessive stress in the pipe. Over time, sand bedding often migrates away from beneath the pipe. However, the most severe issue with sand bedding is soil migration.

Settlement of bedding material is unpredictable, difficult to account for, and may lead to excessive stress if the degree of settlement varies significantly between adjacent areas. The amount of settlement varies depending on the choice of bedding material, the type of pipe, diameter of the pipe, and surrounding native material. Second, since the bedding material is uncompacted, there will be some slight settlement of the pipe when the pipe is laid on the bedding.
Trucks blown over i39 install#
PipePillos are lightweight, easy to handle, and easy to install First, if the sand bedding becomes compacted prior to the pipe being placed, it must be loosened by removal and replacement or by scarifying otherwise the pipe may be damaged due to hard spots in the bedding.įigure 3. Sand bedding can be problematic in multiple ways. The pipe is laid directly onto the bedding. Sand bedding is another common support method, which uses an uncompacted layer of select material, usually sand between four and six inches thick. All of which may lead to or contribute to excessive ovality, if not more severe damage to the pipeline like denting. Improper arrangement of sandbags may cause the very thing they are trying to address: hard spots, and point loading. However, the reality on-site is often quite different, with sandbags being haphazardly thrown into the trench resulting in an uneven and inadequate support area. When sandbags are chosen as a support method, a critical assumption is made: the sandbags will be arranged as per the engineered drawings to create a well-formed pipeline support. PipePillos can be tied to the pipe for easy installation When it comes to common support methods such as sandbags or sand bedding, they present as many issues as they solve.įigure 2. The common denominator when it comes to pipeline ovality during construction is improper, inadequate, or non-existent pipe support. Rocky terrain, frozen soil and even compressed sand bags have often resulted in dents or excessive ovality. Differential settlements has the potential to increase the stress on the pipe and increase the risk of ovaling. It is often difficult and impractical to match the compaction beneath the pipe to that of the consolidated/virgin soil transitions. Areas of soil transitions such as at tie-in welds and road crossing locations are also of concern. Areas of pipe sag or overbend, where it is difficult to match the trench excavation to the exact curvature of the pipe, may result in a lack of support causing excessive stress on the pipe. A major contributor of on-site pipeline ovality is point-loading due to uneven trench bottoms.
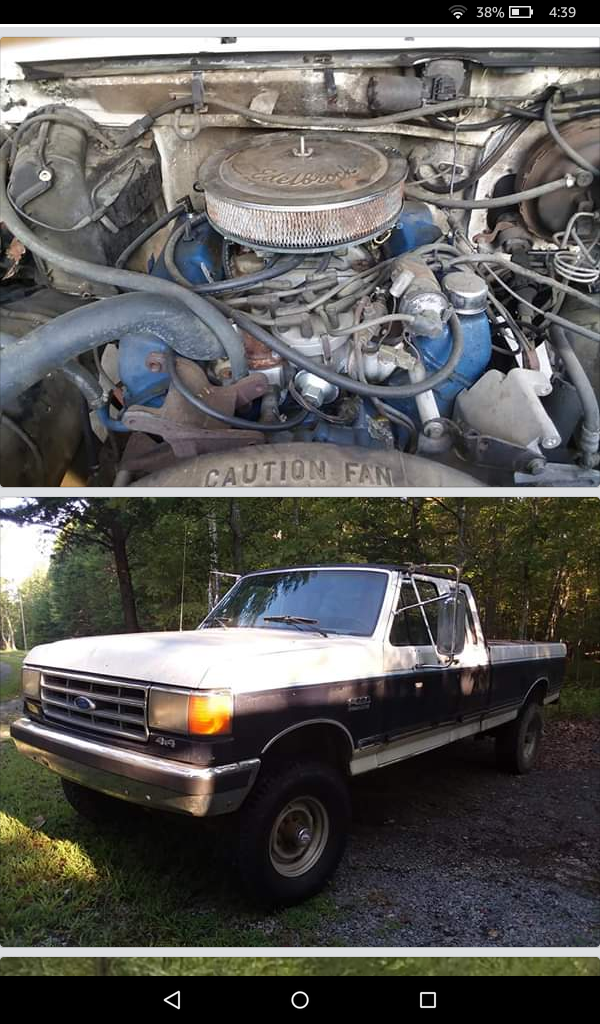
To develop preventative measures, first the common causes of damage, and specifically ovality in the field, must be understood. Although it is important to improve methods of detection and correction of on-site pipe ovality, the most economical and beneficial way of combating pipeline ovality is prevention.įigure 1. There are various methods of detecting and correcting ovality caused during the manufacturing process, but it becomes much more difficult – both to detect and correct – when it happens during the construction phase.

Improper handling and pipe storage, uneven and rocky trench bottoms, and externally applied loads all contribute to an increased risk of pipeline ovality.

However, it is also becoming a more common occurrence on the construction site. Ovality, also referred to as ‘Out of Roundness’ is one of the most common defects in pipe manufacturing. The wide spread use of high strength steels, which allow for thinner walled large diameter pipes, combined with ILI advancements has brought the issue of ovality to the forefront. Like every industry, as improvements are made in one area, challenges may arise in another. More accurate inspection (ILI) equipment, higher strength steels, advancements in cathodic protection, and increased stakeholder engagement have fueled innovation. Technology in the pipeline industry continues to improve year after year.
